Planning Automated Manufacturing
Systems
by
H. F. DICKIE
Manager · Production Control
Material Service, Manufacturing
Services
Currently, the popular approach t6 automatic data processing is
to order a standard, high speed, general purpose computer and then apply
substantial effort and ingenuity to adapt as many routines as possible to
the characteristics of the machine.
Conversely, should we give greater consideration to special purpose
equipments designed to do a particular job more efficiently? The se need
not be single-purpose machines which cannot survive changing business
conditions, but rather might handle a continuing common task like
Inventory Control or Production Scheduling effectively and economically.
This may give us a different viewpoint on the evolution of computer
design. We can look at our own applications not in terms of how they might
be done on a universal or generalized machine, but rather what is the
inherent structure of the manufacturing problem, what are the true needs,
its real requirements? With this approach, we are more inclined to look at
the problem from a systems analysis standpoint, rather than from the
stereotyped let's-mechanize-what we-have-today point of view.
One simple analogy is that of railroad freight cars. Years ago, there
were just a few kinds of freight cars: like the flat car and the box car.
But then some thoughtful transportation men started analyzing true
function and actual needs. So what has been the result? Instead of
offering only the standard cars into which all freight had to be fitted, a
number of special purpose equipments were developed to perform a certain
Job in the best possible way.
For example, some companies wanted protected bulk transportation
for grain and chemical powders; out went the bags, drums
and box cars; in came the covered "hopper
car", designed to do that special Job well. Others wanted store to
door delivery with the advantages of rail shipment. The result: a
"piggy back" car, designed to carry truck trailers with no
intermediate freight handling. Another needed easier and more rapid
loading and unloading. The answer: a car whose whole side looks like a
sliding overhead garage door enabling fork trucks and conveyers to roll
directly into the car.
Another interesting lesson can be learned from the freight cars
analogy; all these cars, though designed to do a specific function, are
planned for integration, they can be joined by standard couplings in any
sequence of reasonable length to make up a whole freight train, together
they may travel throughout the country on standard gauge track.
23·
|
So may our computers, our data processing
devices and our machine contro1s be specialized, yet still be capable of
being coupled together through a common machine-sensible language like
punched cards or magnetic tape. They may be integrated to form a whole
business system.
This coupling, forged from a Common machine language, is needed to
communicate with all the functions of the business, as well as with all
the other businesses and the district offices throughout the
Company. We can even imagine a common machine language with our suppliers
and Our customers. Eyen if this is not completely feasible, we could at
least seek information that is in machine-sensible form, automatically
convertible to use by our computers. We shall also be looking for
translation devices to convert engineering drawings, as Herb Grosch has
mentioned, test instructions and manufacturing operational planning data
directly into machine language.
Next let's look at specific phases of the over-all manufacturing
system. Here is a list of some of our manufacturing functions:
1. Master scheduling
2. Requisition processing
3. Parts explosion
4. Inventory control
5. Purchasing
6. Motion time standards
7. Dispatch rules determination
8. Automatic dispatching
9. Quality analysis
10. Manufacturing operations and feedback
Next, look at the other side of the coin - at the other dimension of
this concept. We feel that for manufacturing processes there are four
different types of computer equipment which might be used to solve these
particular problems:
1. Batch Computation - some processes by their very nature have to be
done in a group. You have to accumulate a certain number of transactions
or activities before going through the computational process. The weekly
payroll or quarterly financial statement are typical examples, although
even here the "real time" advocates point out the prospects for
doing a substantial part of these jobs as the data become available.
2. Real Time Data Processing implies that the computer will keep in
step with the actual events going on in the factory. Like the famous
Norman Rockwell painting "The Gossips", where the direct
reporting is carried on as rapidly as practical. In fact the last picture
shows the feedback to the originator.
24·
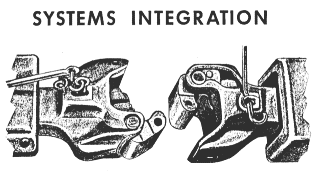
|
3. Machine Controls are used to actually
instruct or operate machine tools, test processes,
or transportation devices practically independent of human intervention.
4. In Simulation a computer is used to act like an actual operating
process. For example, it might be a true imitation of the teal system
simply speeded up or directly scaled down like a model train.
Let's put these two sets of ideas together, manufacturing functions and
types of computers, and then look at the whole picture. For example, the
double check on master scheduling indicates it might best be performed on
a batch basis, though it could also be done on a real-time computer.
Simulation and machine control seem to have little application to waster
scheduling, s0 on through the chart.
Let's start with the first of these areas, the one with which we are
most familiar, Batch Computation. This can be applied either to planning
the system or actual calculation of operating statistics. For example, in
systems planning linear programming could help determine the best traffic
patterns, optimum warehouse locations and most profitable product mix; it
might even be used for directing over-all inventory policy or
manufacturing cycle time determination. Similar computational areas are:
ABC inventory analysis, collation chart preparation, and long-range load
analysis.
One of the interesting operating problems which has been ingeniously
solved on a batch basis is that of inventory control - Otis Elevator has
purchased a special inventory control computer from the Nuclear
Development Corporation of America (NDA). This machine is designed to
operate each night to incorporate all the transactions and activities
which occurred during the day. Processing some 20,000 transactions against
35,000 stock accounts each day would have required an extremely large
random access memory. The solution was a newly developed tape processing
machine which first sorts all the transactions into sequence and then runs
the new transaction tape and waster perpetual inventory tape in parallel
to recalculate the current status.
Another process which might lend itself to batch computation is that of
setting motion time standards. I can conceive of a machine tool wired to
do its own time study, keeping track of its own movements and the elapsed
time for each. But there might be a better way of semi-automatically
setting time standards, using predetermined time standards like M. T. S.
(motion time survey). We could have the time study man use a special
keyboard to record the various basic motions which need to be performed to
accomplish a particular task. This device could prepare a punched paper
tape which would then be fed into a small special purpose computer having
in its memory the standard times for each work element; then with merely a
summary operation these times could automatically be added together and
another time study would be ready for review.
25.
|
Another area which may require batch
computation is that of production master scheduling. Production Control
Service worked with the General Engineering Laboratory in the development
of a special scheduling computer called PRODUCTRON, which incidentally is
now being manufactured and sold by the Industrial Computer Section. This
is an analog machine designed to do load analysis of 50 products on 24
work stations for a single time period.
While this is fine for certain departments' problems, it is of course
too small to handle many others. The answer may be the PRODUCTRON, Sr.
which would be designed particularly for the multitime period problem. One
of the dangers here is that for each additional period covered, the
problem becomes more complex as the square of the number of time periods.
For example, if we use an index of one for the complexity of the single
period problem, a five-time-period situation would be five squared or 25
times as complex.
In discussing real time data processing, let us consider the area that
has received primary attention in the past - that of machine and process
operations control. We in Manufacturing feel that the large business
machine companies have in the past misunderstood the true nature of the
manufacturing or production control data processing function. Production
is a dynamic function, one that lives and breathes in rhythm with the
actual physical processes in the shop. Many of our functions must either
keep pace or fall hopelessly behind. This dynamism is an important
concept, for it implies that machines must frequently operate in real
time, on the line; that machines must make decisions; that machines must
keep track of progress; that machines must talk to machines. This dynamism
plus manufacturing's central location in the business system leads to a
unique problem. Since virtually all the business systems' inputs -
requisitions, engineering lists, and planning records - pass through
manufacturing hands, we are naturally concerned with their accuracy. We
have a direct interest in the machine language used for their preparation
and ease of file maintenance. In turn, we work on this data to prepare
products for sale; we schedule, load, prepare purchase orders, factory
paperwork, dispatch the jobs. move them into and out of stock rooms, pack
and ship them, and prepare shipping papers. The output of our
manufacturing processes feed to finance for their periodic reviews and
analyses. We have the responsibility and the necessity for transmitting
costs, quantity, and quality information.
Looking at this whole picture then we feel that unless manufacturing
can keep up with the shop processes, we are inherently putting a
restriction, a barrier in the path of the other functions' efforts to
mechanize. If, for instance, we only provide cost data once a week, the
cost system can be no better than a weekly process.
One specific "real time" idea which demonstrates clearly the
kind of approach we will make in manufacturing automation is that of
dispatch control. This will illustrate how progress can be realized
reaching ever higher and higher levels of automation. The first step might
well be a specialized computer designed to help the dispatcher by
calculating instantaneously relative priorities of all
26.
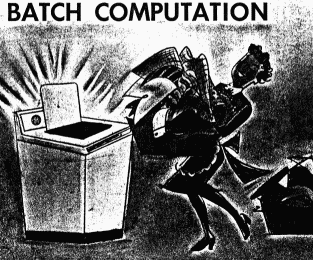
|
the factory jobs at a certain station. And
at least for some time the dispatcher would be needed to evaluate the
unusual and the stochastic or unpredictable elements to be certain that
all factors are properly considered. At some point in time when all these
special factors were adequately known and understood, it may well
be possible to build up these decision processes into a machine and
hook up a device s0 that the machine operator could insert his own
particular key or ,late and have it printed out for him a voucher and work
instruction. This step will eliminate the dispatcher.
The final step might come with the elimination of the machine operator
so that the dispatch device communicates directly with the machines
themselves, picking out the Job with the best priority and issuing
computer sensible instructions and actually starting, directing operations
and stopping the machine.
This automatic dispatcher will have many advantages. Among these
are the ability to consider alternate machines, alternate sequences, lap
phasing and adjustment of economical order quantities.
Even our purchase order preparation can be automated on an online or
real time basis. Visualize purchasing being informed through a
communications network of individual parts requirements from each of the
ordering functions. These would merely detai1identification number,
quantity, and date needed. As each requirement was received, a random
access memory device could be scanned for that particular item to find out
the vendor assignment pattern. The vendor could be picked out, and the
purchase order typed, using the supplier and item information contained in
memory. A further refinement which might be worth
investigation is the idea of direct transmission of orders to offices
right in the same city as the vendor.
The third area for computer equipment is that of direct machine
control, which will actual1y operate machines, giving them their
instructions, measuring their performance and correcting their adjustment.
These machine controls will be used in many areas. We shall need
devices to program "test" operations as well as "make"
operations, process steps as well-as assemb1y steps, packaging and
loading, stock-keeping and receiving. All these electronically controlled
operations will receive internal feedback and be directly governed by
their own instruction readers.
An example with which most of you are familiar is the Giddings and
Lewis tape controlled milling machine. GE built the tape control device
for this machine, which is used for contouring of airplane wings whose
shapes are very complicated. TO be added in the future is some sort of a
control feedback of actual performance to insure that the machine is
following the tape recorded plan.
Another area is that of quality control. We visualize testing machines
more elaborate than those being built today which are programmed to
perform all the tests required and to reject those falling outside of
control limits. In addition, it will analyze these test results in terms
of causative factors and prepare necessary control charts, signal the
faulty input areas, adjust those
27.
|
machines operating out of tolerance, and
calculate a quality performance for purchased parts even though they way
be used in a variety of devices.
There will also be superimposed en the factory a comprehensive feedback
system. This might be similar to I.B.M.'s newly announced Automatic Production
Recording System, which enables certain devices, attached to machines Or
placed on conveyer lines, to signal a central location on quantity counts,
liquid flow, voltage variance, weights, etc. All these figures, even if
measured in analog form, can be converted to digital language for computer
use. We might use this same idea to feedback quality data, cost data, and
process performance statistics.
As someone astutely asked Herb Grosch, a number of new ideas on machine
controls may be obtained by looking at various process industries, since
they have gone so much further than we toward automatic
systems analysis and monitoring. There, even with facilities far separated
physically one from the other, electrical connections permit central
control, central scheduling and central reporting.
The fourth and possible the most interesting area is that of simulation
whereby the computer can be used to "act like" some operating
process. For instance, we can visualize a computer that will perform in a
manner similar to a manufacturing Job shop so that we can test dispatch
rules in a fraction of the time, without disrupting normal day-to-day
operations. We can simulate product performance for quality control
testing and evaluation as was done for the Jet Engine Department by the
General Engineering Laboratory. We can test various empirical management
decision rules to see if external changes will influence the likelihood of
successful operation. This same type of simulator can be used for
predicting future sales trends and for determining optimal inventory
balances where sales vary erratically. Production leveling may find a
practical solution with simulated trials of various manufacturing plans.
Another idea is to simulate the traffic arrival pattern to determine the
number of truck docks and receiving employees required at various times.
Simulators, while offering many unusual opportunities, may require
extensive random access memories, since we are dealing with time dependent
problems. One simple example will show what I mean.
The total number of different ways to arrange a schedule of 15 Jobs of
5 operations each is more than 1060 (a one with 60 zeros). Even
if 99 per cent of these arrangements are impossible or not feasible, we
still must deal with the remaining One per cent or 1058 trials. This is
obviously impractical in spite of 70S's, UNIVAC's et alia. So we turn to
the cut and try approach and our method is to try basic, even intuitive,
formulas or rules and study whether there is a significant variation
rather than trying to solve the problem analytically.
The use of simulation rests heavily on the refinement of new operations
research techniques. This means that we in manufacturing must become more
professional in the adaptation of these techniques
28 |
to our manufacturing control problems before
trying to build a computer to solve a specific area.
We are working on one such problem today, that of dispatch rules
determination, This might ase a mixed analog and digital device with both
potentiometers and magnetic cores which would enable us to run speeded up
tests on shop performance, to tryout various rules, different formulas, a
variety of techniques to see which would result in greater efficiency if
installed in the factory, We hope to build a model on a small scale, a
model of manufacturing dispatching business. This model must act enough
like the shop itself to allow us to extrapolate from the test results
obtained. We will try, instead of using the conventional required finish
dates
For control, to use slack times and flow factors to evaluate, as best
we can, the interactions of one Job on another, By proper use of
statistical inference we should be able to prove or disprove certain
assumptions concerning the behavior of the manufacturing system.
We think that this area of operations simulation may offer the
Industrial Computer Section a challenging opportunity for utilizing their
existing knowledge of analog equipment and their grasp of digital
machines in a field which is limited but not yet tapped by the computer
manufacturers.
In the future, we hope we do not have to design our manufacturing
business around general purpose computers. Rather we believe computers can
be designed to fit into specific manufacturing control needs, While there
has been much talk about 'Using data processing equipment in the
manufacturing operation, the plans have too often proved abortive because
the system was not properly designed first. Today most departments
planning an ambitious automation program have recognized this fact and
are, therefore, devoting their time to an intensive
and extensive systems study prior to making any decision on the nature of
equipment for particular applications.
We are personally enthusiastic about the potentialities of automatic
data processing and hope that our own new Manufacturing Control Automation
Systems Project, which we are Just starting, will serve to some extent as
a product planning function for the Industrial Computer Section, and
conversely, we enter into this project with greater confidence of success,
knowing that the need for this kind of equipment has been recognized and
the Industrial Computer Section established. We feel this area of
development is urgent, that present equipments do not cover the span of
industrial requirements and that a mutual study of these problems will be
most rewarding.
One thought on the effect of data processing on the organization
structure. There has been much stimulating discussion of the
centralization of computer or data processing work. We do feel there
will be rearrangements of personnel, differing from the present functional
lines. For example, if even cost and quality analysis belong together,
they will logically merge. However, we feel the trend will be along these
lines of logical operation and organization and data processing as a kind
of work cannot be setup independent of organization structure,
29·
|
This idea of analyzing the business as a
whole in no sense implies that we must also automate the business as a
whole. This approach insures that we will give thorough consideration to
the entire system - to its interactions and interrelationships, with an
over-all concept being developed which weaves together all the objectives
and goals of the entire business.
An integrated systems approach, an over-all business concept must be
the basis for economical, manufacturing automation. Versatility and
flexibility should be inherent in the automata designed We must provide
for growth; we must provide for change. We must provide for adapting
computers to specific situations, and yet with all this, the total
installation costs must be economically justified. The answer here may be
that we shall have to think in terms of savings to the whole business; we
shall think in terms of departments' profits, rather than in terms of
direct out-of-pocket cost of machine applications.
To quote Dean Wooldridge, President of the Ramo-Wooldridge Corporation.
"The lesson that has been learned by government at the cost of many
millions of dollars is that the integrated systems approach is the proper
approach to complex systems; this principle is just as applicable in
business and industry."
30.
|
BACK
TO INDEX OF SPEECHES |
|